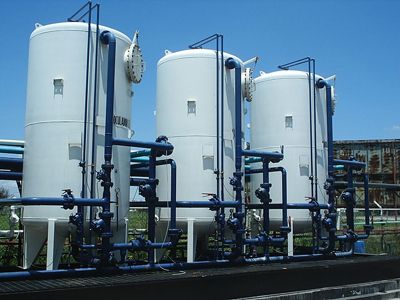
化学镀镍含磷废水处理的工程运行实例
1、工程概述
昆山晶元电子有限公司是一家生产高密度线路板的企业,在生产过程中产生线路板化学镀镍废水,原来该股废水有一套废水系统进行处理,但处理效果不太理想,原有工艺采用铁碳微电解+芬顿氧化+混凝沉淀+离子交换,出水磷和镍的含量一直处在超标状态,2014年,业主委托上海玉畔环保设备有限公司对废水系统进行整改,通过上海玉畔环保设备有限公司组织的专家调研及研发团队的功克,寻找到彻底解决化镍废水的达标的方法。该工程整改从2014年2月开始,于2014年4月完工并顺利运行,运行两年来,排放口检测的镍在0.05ppm以下,总磷含量在0.1ppm以下,数据一直较为稳定,达到了江苏省太湖流域的排放标准。
2、废水水量、水质
2.1处理水量
水量:200m3/d,系统20小时连续运行,平均每小时处理量10m3/h。
2.2 进水要求
要求总磷≤1200mg/l,镍≤100mg/l。
2.3 出水指标
磷≤0.5mg/l,镍≤0.1 mg/l
3、废水处理工艺
本废水处理工艺在原有芬顿氧化+混凝沉淀的基础后增加自己研发的碱性条件下深度破络反应的催化氧化技术,在该技术下,可彻底将镍和次磷做到一级A的标准,以下是工艺流程简图:
3.1 工艺流程简图
3.2 工艺流程简述
废水进入调节池后进行水质水量调节,由提升泵提升至预反应槽,通过调节PH和加入硫酸亚铁达到芬顿氧化的反应条件,预反应槽出水进芬顿氧化池,加入双氧水进行氧化反应,将废水中的次磷氧化成正磷以便去除。芬顿氧化出水加碱调节PH, 去除废水中大量铁离子和磷,再经絮凝池1,加入PAM反应,絮凝后的废水接着进入沉淀池1,沉渣进入含磷污泥池,上清液出水进入中间水池,再通过多效催化氧化器去除难以氧化的有机物,使破络反应更加彻底,经过多效催化氧化作用后,出水再经过调节PH,去除废水中的镍离子,再经絮凝池2,加入PAM反应,絮凝后的废水接着进入沉淀池2,沉淀池2出水后即可达标排放。
4、多效催化氧化技术
多效催化氧化的核心在于复合氧系催化剂,能够利用双氧水在常温常压工艺是对传统的化学氧化法的改进与强化,可以对范围很广的有机物进行无选择氧化,在必要的条件下将会使有机污染物矿化成二氧化碳和水,还可以使无机物氧化或转换。
多效催化氧化,协同三相催化氧化技术,这三相分别是:由风机送入塔内的压缩空气(气相),外加的高效氧化剂(液相),和固定在载体上的催化剂(固相),其中催化剂为复合型贵金属化合物,正是该催化剂的作用,使空气中的氧气也作为氧化剂参与反应,从而减少了液相氧化剂的耗量,降低了处理成本,提高了处理效率,又能使反应速度大大加快,缩短了废水在塔内的停留时间。废水经去除固体杂物后,进入催化氧化塔,在反应中废水中的有机物和氧化剂分子在催化剂表面上经过吸附、催化氧化反应、产物脱附等几个步骤后废水中有机污染物被氧化剂分解,苯环,杂环类有机物被开环,断链,大分子变成小分子,小分子再进一步被氧化为二氧化碳和水,从而使废水中的COD值大幅度降低,色泽基本褪尽,同时提高了BOD/COD的比值,降低了废水毒性,提高了废水的可生化性,为后续生化处理创造条件
多效催化氧化具备以下优越性:
(1)高效催化剂的使用提高了氧化效率,克服了对有机物氧化的选择性,处理效果好。
(2)氧化剂采购制备简便, 投资及运行费用低,与其它处理方法的费用相比,比较低廉。
(3)催化氧化反应在常温常压下进行,反应条件温和,易于操作,设备投资少。
(4)对有机物的降解以生成含氧基团的小分子化合物为主,不产生二次污染物,且在削减COD同时提高了BOD5/COD值,为后续生化处理创造了条件。
(5)催化氧化工艺中的催化剂制备方法可靠,使用寿命长,流失率低,具有高稳定性,并且安装操作简单,运行经济。该工艺*大的优点是可以附加于任何传统处理工艺,因此对高浓度废水原处理工艺的改造有着其他工艺无法比拟的独特优势。
5、工程投资及运行费用
本次工程总投资为67万,含设备,池体,管道电气,安装调试,税收等。本工程采用交钥匙工程,废水建成后,实际运行成本为每吨水8.5元/吨水,运行成本包括电费,药剂废,耗材费用(催化剂2年一更换,每吨水耗费0.2元),人工费等。
6、系统运行效果
工程投建完工,并经调试结束,系统运行一直比较稳定,经过芬顿氧化后混凝沉淀出水总磷小于1mg/L,总镍出水小于0.3mg/L,经过多效果催化氧化出水后,总磷小于0.1mg/L,总镍小于0.05mg/L,并连续一年无超标记录。
7、结论
1、采用传统的芬顿氧化方法无法一次性将废水中的磷和镍做到达标,通过增加多效催化氧化环节,将芬顿氧化无法破络的次磷进一步通过该方法彻底氧化,从而实现磷和镍的分离并通过沉淀去除。
2、现有化镍系统存在不达标的现场,无需做大的改动或使用成本较高的药剂,增加一套多效催化氧化器和混凝沉淀系统即可实现稳定达标。多效催化氧化对整体运行成本增加不大,且催化剂更换周期长,相对耗材费用较少。
3、工艺可靠,无二次污染,无多余污泥或固废产生,工艺环保,运行成本低。